Aerospace Brackets
Lighter-Stronger-Durable

Traditional aerospace engine brackets are typically machined from solid metal blocks (e.g., aluminum or titanium), which leads to:
Excess weight that reduces fuel efficiency and increases emissions
High material waste (up to 90% in subtractive machining)
Complex multi-part assemblies that require fasteners or bonding, adding to labor and failure risks
Long lead times for tooling, fabrication, and post-processing

Our 3D Fiber Tethering 3DFiT solution is to the point.
With 3D Fiber Tethering (3DFiT), we eliminate the constraints:
Printing monolithic composite brackets with no joints or fasteners
Directly steering continuous carbon fibers along optimized load paths to reduce stress concentrations
Removing the need for molds or machining, enabling faster iteration and on-demand production
Supporting topology-optimized designs for truly 3D, structurally efficient geometries
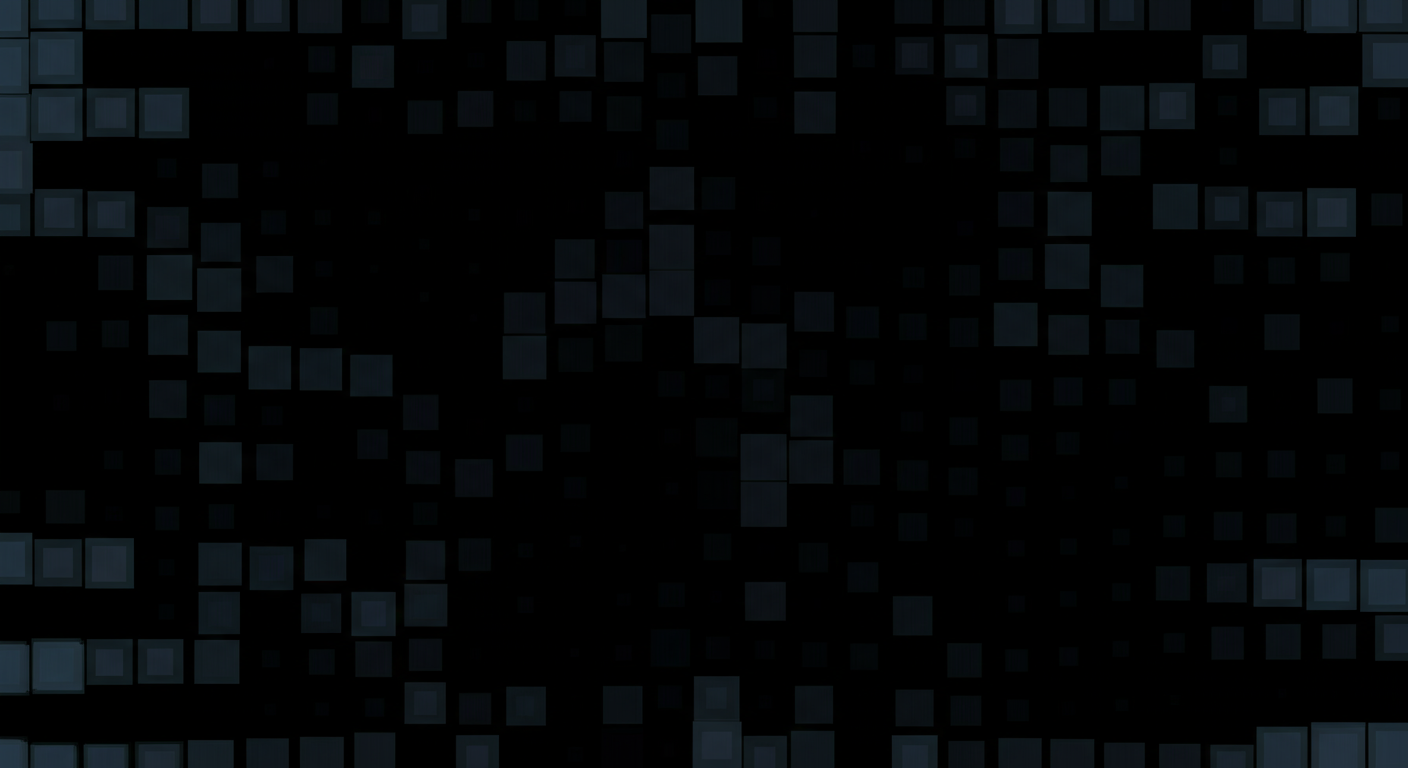
3DFiT offers a transformative path to lighter, stronger, and more efficient engine brackets, supporting the aerospace industry's drive for next-gen sustainability and performance.
Up to 90% weight reduction compared to metal brackets
2–3x higher specific strength and stiffness than aluminum
Seamless integration of fiber paths to avoid delamination and joint failure
Rapid turnaround with zero tooling lead time ideal for both prototyping and flight-ready parts